Vineyards have structure, he points out. “They have rows, poles and common geometry.”
But Mikhail and his mostly Russian team of technicians, now based in Slovenia, have decided to make the challenge tougher by not only designing a robot that can work safely on steep slopes with a total load capacity of two tons, but also design a system that is capable of doing most of the labour-intensive jobs in the vineyard – such as mowing, mulching, harrowing, pesticide spraying, fertiliser spreading, canopy trimming, and, in the future, pruning and harvesting. In all conditions and on slopes up to 42°.
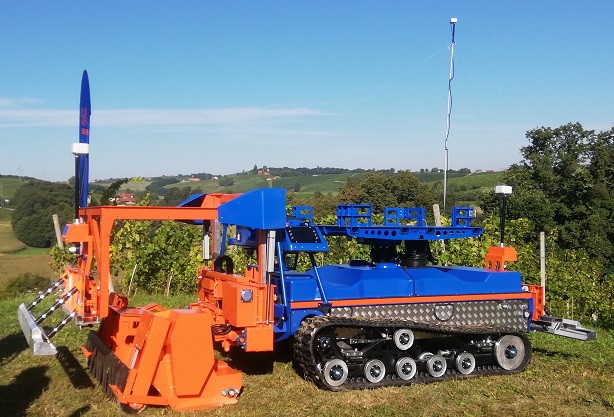
PeK Automotive’s robot, Slopehelper (above), has gone into production in Vrhnika, a small town near Slovenia’s capital, Ljubljana, with the first 16 machines being prepared for large wine producers in Slovenia.
For Mikhail, who gained his PhD from a naval academy at the age of 23, it was important to design a whole system and not just a robot. He says there are many autonomous robotic platforms coming on the market and they all work well – until you connect them to equipment. “Then all work done is useless,” he says in his heavy Russian accent.
PeK Automotive has been developing a system to support all vineyard activity. “That’s the dramatic difference between ours and others,” Mikhail says. “We are working not for developing of robot, we are developing for complex system covering everything. The system includes navigation, hinged equipment, some mapping and so on. We’re not doing some small part.”
I point out that if vineyard owners have to abandon the equipment they already own to purchase the special tools for the Slopehelper, it’s going to be expensive. What’s wrong with developing a machine that can use existing equipment?
‘It’s like taking a microscope to nail’“The most obvious and logical way is usually wrong, that’s the law of life,” Mikhail replies. “This is exactly this case. The absolutely logical thinking is, ‘I have all this equipment, I must make a machine and I will connect them and everything will be okay’. Sorry, it won’t be... It’s like taking a microscope to nail something. When you are working with tractor the eyes of the equipment are your eyes, but the equipment itself is blind… Robot has no eyes, it has sensors. If equipment isn’t equipped with sensors, the robot will never know what is going on and what is necessary to do this millisecond.”
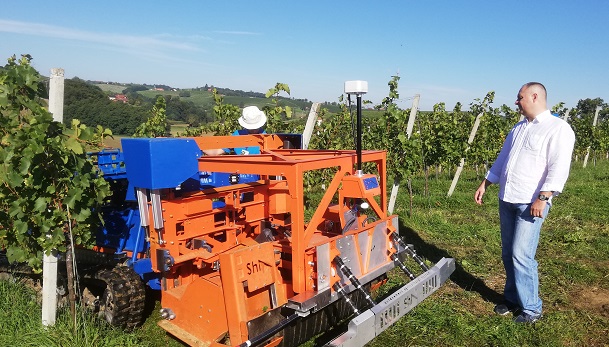
Mikhail (above) admits Slopehelper is a “very ambitious” project. He’s talking to me as we watch the chunky machine trundle down a long row of vines. It has a maximum speed of 10km/hr, but it appears to be going much slower. The row is about 300m in length. It takes ages before the caterpillar-tracked machine turns and comes back between the next row of vines.
But one advantage of a robot is that speed and time are less crucial. The robot can be programmed to go at a safe speed, where it can stop immediately its radars at the front, rear or sides detect anything that shouldn’t be there. These radars, Mikhail says, can also be used to detect the ripeness of the fruit.
The slow demonstration gives Mikhail time to talk to me about all the special equipment his team is developing for the Slopehelper. They are currently testing a trimmer for the tops and sides of the canopy; they are developing hinged equipment especially for terraced vineyards; they are developing an under-vine cultivator that won’t damage young plants. And, most interestingly, they are developing something that sounds a bit like Edward Scissorhands to prune and harvest grapes. It will have a rotating head with four scissors.
“No shaking,” Mikhail points out, “it’s like hands.”
It will cut each bunch separately while travelling at about 150mm per second.
“The same system will be used for pruning, but pruning will be much less intellectual than people is doing, of course, because it will be based on measurement of thickness (of shoots and canes). So quality, I guess, will be 60-70% from manual one.”
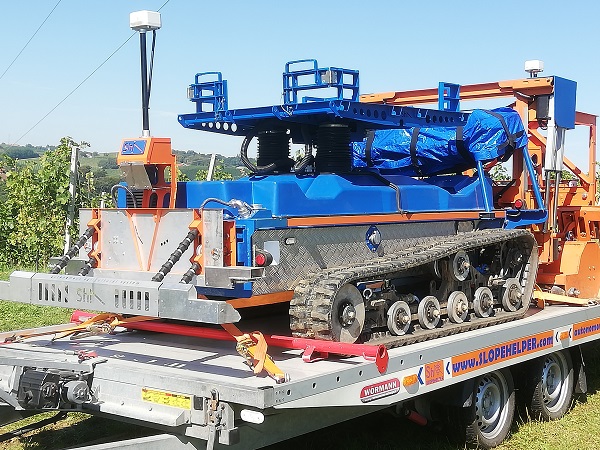
The machine’s benefits
- The combination of electric propulsion, radars and artificial intelligence (using an algorithm to recognise and adapt to new situations rather than relying on a GPS signal to find its way around a vineyard).
- Being light enough to transport to the field on a regular trailer (above).
- Yet it is tough. It’s a derivative of a rugged amphibious vehicle, the Vanquisher, developed in Russia for the niche market of rescuers, firefighters, and foresters. With the transmission located inside the sealed body, Slopehelper can work in a muddy or dusty vineyard.
- Slopehelper’s self-stabilising horizontal cargo platform (on top of the body), wide caterpillars and powerful construction mean it can handle steep slopes safely while carrying liquids for spraying or two tons of harvested fruit. Thanks to the vertical gravity axis always being in the centre of the vehicle, the harvesting bin and loads are always held horizontally in every direction. Mikhail points out that it’s also safer to use an autonomous vehicle on slopes: “A lot of tractor accidents take place on slopes. Unfortunately, it will continue happening because humans will continue taking risky decisions… The huge advantage of our vehicle is that it is a machine – it is not a human, it cannot get tired, and will not take risks.”
- Slopehelper can navigate wet soil and operate in all weather conditions.
- It can work with two types of hinged equipment at the same time. This means it can work with a mulcher at the front, for example, and a sprayer at the rear.
- The robot uses 24kWh-capacity lithium batteries. This allows the machine to operate at full load (40° inclination and constant traction force of 2 tons per load) for up to 6 hours (8 hours with a 36kWh pack). In standard mode, it can operate for more than 14 hours.
It offers a range of control options:
- Autonomous mode – for everyday operations, with the vehicle automatically moving along the rows and performing its tasks.
- Semi-autonomous mode – to assist with harvesting, for example, with the operator pressing two buttons to move the vehicle forward or back.
- First-person view – a motorised camera allows the operator to view the situation remotely, observing the machine’s performance in real time.
- Visual remote control – operators can take command of Slopehelper remotely.
- Follow Me mode – a special ultrasonic beacon is placed on the operator’s shoulder and the machine obediently follows them around the vineyard.
Price of Slopehelper is around €95,000 for a machine with some key pieces of equipment. Delivery time is three to five months.
It’s not the sleekest-looking machine and doesn’t have the most aesthetically pleasing colour scheme, but it does appear to be solid, sturdy and functional.
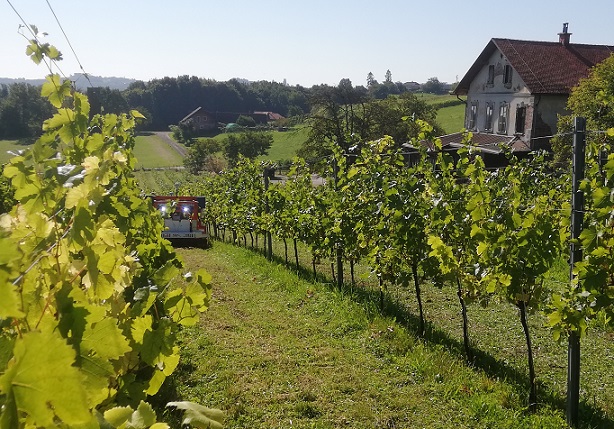
I attended a demonstration at one of sparkling wine producer Radgonske Gorice’s vineyards in northeast Slovenia. This 4ha organic site produces indigenous grape variety Ranina for a pét-nat.
Two Slopehelpers turned up for the demonstration on trailers pulled by pick-ups. Each machine measures 260cm in length, 160 wide and 130 high. It weighs 1,750kg.
The PeK technicians used remote control units to guide the machines off their trailers and to their starting points. One was used to show how it deals with slopes; the other was used to show how it negotiates a long row, turns at the end and comes back down the next row (above).
The key parameters of the task were input via a built-in interface. The first Slopehelper then set off down the slope, automatically turning around at the end, then heading back up the slope along the next row. The caterpillar tracks did churn up the soil on the headlands as the vehicle manoeuvred into position for the next row. Doing alternate rows would easily solve this problem.
Both demonstrations, however, came to abrupt halts – but for different reasons. The steep-slope demonstration stalled when the robot’s radars, constantly scanning the area up to 30m away, detected a potentially dangerous obstacle. It turned out to be an out-of-line old vine, but the machine’s onboard computer had to be reset to override the shutdown. In a customer’s vineyard, the system’s artificial intelligence will help it get to know the configuration of the vines.

The second demonstration, in the vineyard’s longest rows, stopped about two-thirds of the way along the return leg. The reason this time was signal confusion, with a reflection of the beam from the other machine (it’s the first time they had run two machines in the same vineyard).
“We placed the second machine in front of the base station. It was a mistake,” Mikhail confesses.
The downtime, though, gave me the chance to ask one more question…
What’s next?
“We are planning to downscale the Slopehelper for small vineyards and orchards – of 2-3 hectares.”
Application: vines (row width >200cm)
Dimensions: length 260cm, width 160cm, height 130cm
Weight: 1750kg (payload up to 2000 kg)
Energy: 100% electrical (Lithium batteries)
Autonomy: up to 14hrs
Traction: caterpillar drive, slopes up to 45°
Navigation: autonomous location system algorithms of row’s detection
Pulling force: over 20kN
Speed: max. 10km/hr
Other: communication remote control, camera and mobile app TeroAir